To address the needs of aerospace OEMs and their suppliers for quality airflow measurement in both aircraft and land-based turbine engine components, the design and implementation of airflow test systems must meet several critical requirements:
- Accuracy: Ensuring that measurements are precise and reliable to maintain high performance and safety standards in engine components.
- Repeatability: The test systems should deliver consistent results across multiple tests.
- Throughput: The systems must be efficient to handle high volumes of tests, accommodating the rigorous production schedules turbine engine manufacturers.
- Availability: The test systems should be readily available and adaptable to meet the specific requirements of each OEM’s unique testing specifications.
Given that, these systems must comply with the diverse in-house testing procedures of major industry players, including:
- GE Aerospace (formerly GE Aviation)
- GE Vernova (formerly GE Power and GE Energy)
- Honeywell Aerospace
- Mitsubishi Power
- Mitsubishi Heavy Industries
- Pratt & Whitney America & Canada
- Rolls-Royce
- Solar Turbines
- Siemens Energy
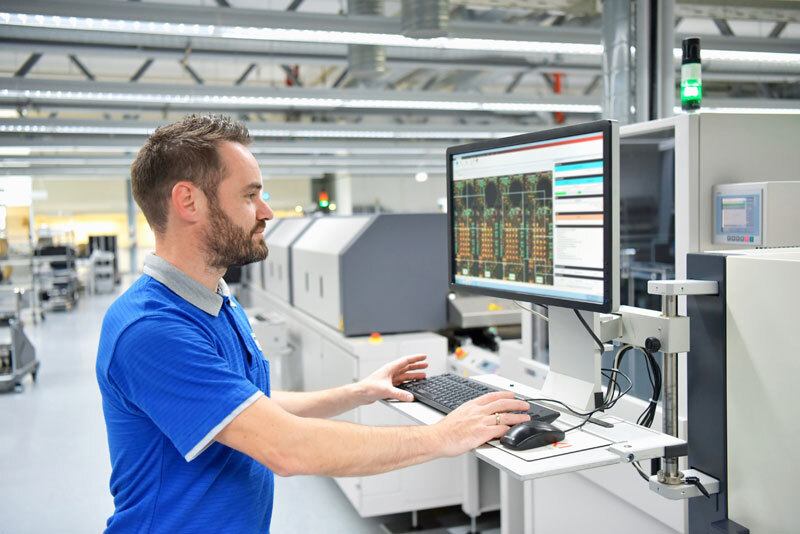
It’s important for these test systems to be designed with flexibility in mind. This means incorporating modular and adaptable components that can be adjusted to fit varying test requirements. The ability to configure the systems to different testing protocols, standards, and specifications will be essential for ensuring compliance and meeting the expectations of each OEM and/or supplier.
Developing such versatile and high-performing test systems often involves advanced technologies in measurement instrumentation, data acquisition, and control systems. Additionally, collaboration with OEMs to understand and integrate their specific testing requirements can further enhance the effectiveness and efficiency of the airflow measurement systems.
OneFLOW’s TS-1000 can set a pressure or flow rate at the test piece utilizing the OneFLOWArray™ of sonic nozzles and OneFLOW+™ software to measure the user defined parameter (such as Effective Area or Flow Parameter). Once the process achieves steady state flow, the resultant parameter is recorded, evaluated for pass/fail, and the data is saved. All pressure, temperature, and flow measurements are National Institute of Standards and Technology (NIST) traceable.
Standard test pressures range from 20 inwc (5 kPa) to 20 psig (1.4 bar). Standard flow rates range from 0.00026 to 1 lbm/sec (0.00011 to 0.45 kg/s). Please call for other pressure and flow ranges.
Accuracies: 0.11% to 0.50% of reading on Mass Flow are available.
*Pictures coming soon